- Consolidated fourth quarter Sales of $140.4 million compared to $106.4 million in the prior year
- Quarterly Net Income of $5.6 million and EPS of $0.14
- EBITDA of $16.5 million compared to $15.3 million in the prior year quarter
- Growth strategy continues with $52.7 million in capital spending and $57.6 million in cash deployed for the Halex acquisition in fiscal 2022.
- Quarterly dividend of $0.105 per common share to be paid December 30, 2022
TORONTO, Nov. 29, 2022 (GLOBE NEWSWIRE) — Exco Technologies Limited (TSX-XTC, OTCQX-EXCOF) today announced results for its fourth quarter and year ended September 30, 2022. In addition, Exco announced a quarterly dividend of $0.105 per common share which will be paid on December 30, 2022 to shareholders of record on December 16, 2022. The dividend is an “eligible dividend” in accordance with the Income Tax Act of Canada.
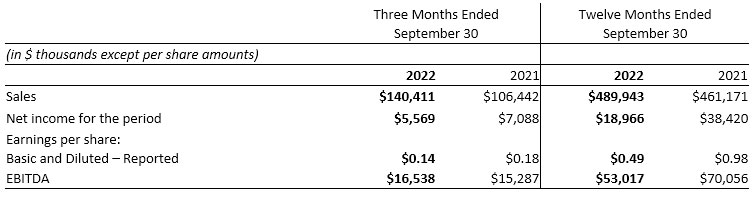
“In F2022 we continued to build on the foundation that will provide Exco with significant growth opportunities in the years to come”, said Darren Kirk, Exco’s President and CEO. “I want to thank all of our employees for their hard work and commitment to always working safely as we help power the electric vehicle revolution and contribute positively towards the worldwide movement of reducing emissions.”
Consolidated sales for the fourth quarter ended September 30, 2022 were $140.4 million compared to $106.4 million in the same quarter last year – an increase of $34.0 million, or 32%. Foreign exchange rate movements were negligible reducing sales by $0.6 million in the quarter.
The Automotive Solutions segment experienced a 16% increase in sales, or an increase of $9.2 million, to $66.0 million from $56.8 million in the fourth quarter of 2021. Excluding the impact of foreign exchange, segment sales increased $10.1 million, or 18%. The sales increase was driven by higher vehicle production volumes and fewer program launch delays as supply chain disruptions eased in the quarter. North American vehicle production was up 24% compared to a year ago and European vehicle production was up 20%. Sales increased at all four of the segment’s operations as we benefited from higher production volumes and the continued ramp up in new programs. This outweighed negative mix and lost shipping days at Neocon which was impacted by Hurricane Fiona at year end. Looking forward, OEM vehicle production volumes are expected to increase as the semiconductor chip shortage continues to improve. While industry growth may be tempered by rising interest rates and emerging indicators of a global recession, there remains significant pent-up customer demand for new vehicles and dealer inventory levels are expected to be replenished from historically low levels. As well, Exco will benefit from recent and future program launches that are expected to provide growth in our content per vehicle. Quoting activity remains encouraging and we believe there is ample opportunity to achieve our targeted growth objectives.
The Casting and Extrusion segment recorded sales of $74.4 million in the fourth quarter compared to $49.6 million last year – an increase of $24.8 million or 50%. Excluding the impact of foreign exchange movements, the segment’s sales were up 47% for the quarter. Included in the quarter was the first full quarter of Halex sales. Halex sales of $12.3 million were up compared to Q3, but remained below potential due to European summer holidays and the Russian conflict in Ukraine and weakening economic conditions in Europe. Demand for our extrusion tooling (ie dies, dummy blocks, stems, etc) and associated capital equipment (die ovens, containers, etc) outside of Europe remained strong due to both industry growth and ongoing market share gains. Management remains focused on standardizing manufacturing processes, enhancing engineering depth and centralizing some support functions across its various plants. These initiatives have reduced lead times, enhanced product quality, expanded product breadth and increased capacity, all of which has supported market share gains. In the die-cast market, which primarily serves the automotive industry, demand and order flow for new moulds, associated consumable tooling (shot sleeves, rods, rings, tips, etc) and rebuild work has recently picked up as industry vehicle production recovers and new electric vehicles and more efficient internal combustion engine/transmission platforms are launched. As well, customer inventory levels have begun to be rebuilt as expectations for higher vehicle production volumes improves. In addition, demand for Exco’s industry leading additive (3D printed) tooling has continued to gain significant traction as customers focus on greater efficiency with the size and complexity of die cast tooling continuing to increase. Sales in the quarter were also aided by price increases, which were implemented in order to protect margins from higher input costs. Quoting activity remains very robust and our backlogs remain firm, which is expected to bode well for sales into fiscal 2023.
The Company’s fourth quarter consolidated net income decreased to $5.6 million or earnings of $0.14 per share compared to $7.1 million or earnings of $0.18 per share in the same quarter last year – a decrease of 22%. The effective income tax rate was 26% in the current quarter compared 27% in the same quarter last year.
Fourth quarter pre-tax earnings in the Automotive Solutions segment totalled $6.5 million, an increase of $2.0 million or 44% over the same quarter last year. Fourth quarter Automotive sales are traditionally lower due to summer shutdowns and in the current year our quarterly sales increased due to a reduced impact of the semiconductor shortage and new product launches. Nonetheless, some of our plants continued to experience disruptions by the semiconductor shortage, which can continue to be unpredictable, making it very difficult to manage operations efficiently. Our plants often build products based on releases only to be informed of cancelations or delays. Other times, releases would be accelerated causing our operations to work overtime and incur expedited shipping costs. These production and shipping challenges also created inefficiencies that increased overhead and direct labour costs during the quarter. As discussed earlier, Neocon was shutdown for 3 days due to the impact of Hurricane Fiona which negatively impacted the segment’s pretax profit. Management is cautiously optimistic that its overall cost structure will return to relatively normal levels in future quarters as scheduling and predictability improves with strengthening volumes.
Fourth quarter pre-tax earnings in the Casting and Extrusion segment totalled $2.6 million, a decrease of $3.4 million or 57% over the same quarter last year. The pretax profit decline was driven by $2.2 million higher depreciation, start-up costs at Castool Morocco and Castool’s heat treatment operations in Newmarket, temporary outsourced heat treat costs in Markham as new equipment is installed, and higher raw material, freight and labour costs due to inflation. Many of these costs are one-time or temporary costs. Management expects to generate higher sales or eliminate these costs over the coming quarters through efficiency improvements and has taken pricing action to recapture lost margin where possible. The higher depreciation relates to Halex and the Company’s investment in new capital that will improve operations and provide access to new geographies to increase our market share. Many of these assets became “ready for use” in the quarter, without realizing the improvements in operating efficiencies and or higher sales. The Castool Morocco ramp is proceeding favorably, but has been slower than anticipated due to the supply chain constraints, inflation, and the Russian invasion of Ukraine.. Management remains focused on reducing its overall cost structure and improving manufacturing efficiencies and expects such activities together with its sales efforts should lead to improved segment profitability over time.
The Corporate segment in the fourth quarter recorded expenses of $0.1 million compared to $0.7 million last year due to foreign exchange gains and lower compensation expenses in the current quarter. As a result of the foregoing, consolidated EBITDA in the quarter was $16.5 million (11.8% of sales) compared to $15.3 million (14.4% of sales) last year.
Operating cash flow before net changes in working capital was $17.5 million in the quarter compared to $15.3 million in the prior year quarter. Lower fourth quarter net income was offset by increased depreciation, amortization and interest costs in the current quarter. The negative change in working capital in the current quarter reflects higher accounts receivable and inventory due to strong business activity as well as the addition of Halex and Castool Morocco. Investment in fixed assets of $16.3 million includes $10.5 million in growth capital expenditures related to the Company’s strategy to increase capacity, add innovative equipment for new processes, and address customer demand in existing and new locations. These projects include: a) Investment in new heat treatment equipment in the tooling group to increase capacity, reduce emissions and enable us to in-source most of our requirements. b) Investments in the Large Mould group to upgrade its capabilities to handle moulds of extreme sizes which we expect will be increasingly demanded by most traditional and new OEMs. c) Investment in additional 3D printing machinery in our tooling group to meet strong customer demands. d) Finalize the expansion of two of our production facilities in the Automotive Solutions group to provide added capacity for awarded programs. Exco ended the quarter with $90.3 million in net debt. The Company has $20.0 million in available liquidity under its banking facilities at year end and on November 7, 2022 the Company increased its credit facilities by $25 million to $152 million with no changes in terms.
Outlook
Despite current macro-economic challenges, including tightening monetary conditions, the overall outlook is very favorable across Exco’s segments into the medium term. Consumer demand for automotive vehicles is currently outstripping supply in most markets, which are constrained by a shortage of semiconductor chips and, to a lesser extent, other raw materials, components and availability of labour. Dealer inventory levels, although increasing slightly, are near record lows, while average transaction prices for both new and used vehicles are at record highs and the average age of the broader fleet has continued to increase to an all-time high. This bodes well for higher levels of future vehicle production and the sales opportunity of Exco’s various automotive components and accessories once supply chains normalize. In addition, OEM’s are increasingly looking to the sale of higher margin accessory products as a means to enhance their own levels of profitability. Exco’s Automotive Solutions segment derives a significant amount of activity from such products and is a leader in the prototyping, development and marketing of the same. Moreover, the rapid movement towards an electrified fleet for both passenger and commercial vehicles is enticing new market entrants into the automotive market while causing traditional OEM incumbents to further differentiate their product offerings, all of which is driving above average opportunities for Exco.
With respect to Exco’s Casting and Extrusion segment, the intensifying global focus on environmental sustainability is creating significant growth drivers that are expected to persist through at least the next decade. Automotive OEMs are looking to light-weight metals such as aluminum to reduce vehicle weight and reduce carbon dioxide emissions. This trend is evident regardless of powertrain design – whether internal combustion engines, electric vehicles or hybrids. As well, a renewed focus on the efficiency of OEMs in their own manufacturing process is creating higher demand for advanced tooling that can contribute towards their profitability and sustainability goals. Certain new EV manufacturers have adopted the approach of utilizing much larger die-cast machines to cast entire sub-frames of vehicles out of an aluminum based alloy rather than assemble numerous pieces of separately stamped and welded pieces of ferrous metal. Traditional OEMs have started to adopt this trend and Exco is positioning its operations to capitalize accordingly. Beyond the automotive industry, Exco’s extrusion tooling supports diverse end markets which are also seeing increased demand for aluminum driven by environmental trends, including energy efficient buildings, solar panels, etc.
On the cost side, inflationary pressures remain elevated while prompt availability of various input materials, components and labour remains challenging. We are offsetting these dynamics through various efficiency initiatives and taking pricing action where possible although there is typically several quarters of lag before the counter measures are evident.
The Russian invasion of Ukraine has added additional uncertainty to the global economy. And while Exco has essentially no direct exposure to either of these countries, Ukraine does feed into the European automotive markets and Europe has significant dependence on Russia for its energy needs.
Exco itself is also looking inwards with respect to ESG and sustainability trends to ensure its own operations are sustainable. We are investing significant capital to improve the efficiency and capacity of our own operations while lowering our own carbon footprint. Our Sustainability Report is available on our corporate website at: www.excocorp.com/leadership/sustainability/.
Exco is currently targeting a compounded average annual growth rate (excluding acquisitions) of approximately 10% for revenues and slightly higher levels for EBITDA and Net Income through fiscal 2026, which is expected to produce an annual EPS of roughly $1.90 by the end of this timeframe. This target is expected to be achieved from organic means through the launch of new programs, general market growth, and also market share gains consistent with the Company’s operating history. Capital investments will remain elevated in the balance of the fiscal year in order to position the Company for the significant growth opportunities we see.
For further information and prior year comparison please refer to the Company’s Third Quarter Financial Statements in the Investor Relations section posted at www.excocorp.com. Alternatively, please refer to www.sedar.com.
Non-IFRS Measures: In this News Release, reference may be made to EBITDA, EBITDA Margin, Pretax Profit, Free Cash Flow and Maintenance Fixed Asset Additions which are not defined measures of financial performance under International Financial Reporting Standards (“IFRS”). Exco calculates EBITDA as earnings before interest, taxes, depreciation and amortization and EBITDA Margin as EBITDA divided by sales. Exco calculates Pretax Profit as segmented earnings before other income/expense, interest and taxes. Free Cash Flow is calculated as cash provided by operating activities less interest paid and Maintenance Fixed Asset Additions. Maintenance Fixed Asset Additions represents management’s estimate of the investment in fixed assets that are required for the Company to continue operating at current capacity levels. Given the Company’s elevated planned capital spending on fixed assets for growth initiatives (including additional Greenfield locations, energy efficient heat treatment equipment and increased capacity) through the near term, the Company has modified its calculation of Free Cash Flow to include Maintenance Fixed Assets and not total fixed asset purchases. This change is meant to enable investors to better gauge the amount of generated cash flow that is available for these investments as well as acquisitions and/or returns to shareholders in the form of dividends or share buyback programs. EBITDA, EBITDA Margin, Pretax Profit and Free Cash Flow are used by management, from time to time, to facilitate period-to-period operating comparisons and we believe some investors and analysts use these measures as well when evaluating Exco’s financial performance. These measures, as calculated by Exco, do not have any standardized meaning prescribed by IFRS and are not necessarily comparable to similar measures presented by other issuers.
Quarterly Conference Call – November 30, 2022 at 10:00 a.m. (Toronto time):
To access the listen only live audio webcast, please log on to www.excocorp.com, or https://edge.media-server.com/mmc/p/zrnzwzys a few minutes before the event. Those interested in participating in the question-and-answer conference call may register at https://register.vevent.com/register/BIada00dd72114489380007ae964528b65 to receive the dial-in numbers and unique PIN to access the call. It is recommended that you join 10 minutes prior to the event start (although you may register and dial in at any time during the call). For those unable to participate on November 30, 2022, an archived version will be available on the Exco website until December 14, 2022.
Source: | Exco Technologies Limited (TSX-XTC) |
Contact: | Darren Kirk, President and CEO |
Telephone: | (905) 477-3065 Ext. 7233 |
Website: | https://www.excocorp.com |
About Exco Technologies Limited:
Exco Technologies Limited is a global supplier of innovative technologies servicing the die-cast, extrusion and automotive industries. Through our 20 strategic locations in 9 countries, we employ approximately 5,000 people and service a diverse and broad customer base.
Notice To Reader: Forward Looking Statements
This press release contains forward-looking information and forward-looking statements within the meaning of applicable securities laws. We may use words such as “anticipate”, “may”, “will”, “should”, “expect”, “believe”, “estimate”, “5-year target” and similar expressions to identify forward-looking information and statements especially with respect to growth, outlook and financial performance of the Company’s business units, contribution of our start-up business units, contribution of awarded programs yet to be launched, margin performance, financial performance of acquisitions, liquidity, operating efficiencies, improvements in, expansion of and/or guidance or outlook as to future revenue, sales, production sales, margin, earnings, earnings per share, including the outlook for 2026, are forward-looking statements. These forward-looking statements include known and unknown risks, uncertainties, assumptions and other factors which may cause actual results or achievements to be materially different from those expressed or implied. These forward-looking statements are based on our plans, intentions or expectations which are based on, among other things, the current improving global economic recovery from the COVID-19 pandemic and containment of any future or similar outbreak of epidemic, pandemic, or contagious diseases that may emerge in the human population, which may have a material effect on how we and our customers operate our businesses and the duration and extent to which this will impact our future operating results, the impact of the Russian invasion of Ukraine on the global financial, energy and automotive markets, including increased supply chain risks, assumptions about the number of automobiles produced in North America and Europe, production mix between passenger cars and trucks, the number of extrusion dies required in North America and South America, the rate of economic growth in North America, Europe and emerging market countries, investment by OEMs in drivetrain architecture and other initiatives intended to reduce fuel consumption and/or the weight of automobiles in response to rising climate risks, raw material prices, supply disruptions, economic conditions, inflation, currency fluctuations, trade restrictions, energy rationing in Europe, our ability to integrate acquisitions, our ability to continue increasing market share, or launch of new programs and the rate at which our current and future greenfield operations in Mexico and Morocco achieve sustained profitability. Readers are cautioned not to place undue reliance on forward-looking statements throughout this document and are also cautioned that the foregoing list of important factors is not exhaustive. The Company will update its disclosure upon publication of each fiscal quarter’s financial results and otherwise disclaims any obligations to update publicly or otherwise revise any such factors or any of the forward-looking information or statements contained herein to reflect subsequent information, events or developments, changes in risk factors or otherwise. For a more extensive discussion of Exco’s risks and uncertainties see the ‘Risks and Uncertainties’ section in our latest Annual Report, Annual Information Form (“AIF”) and other reports and securities filings made by the Company. This information is available at www.sedar.com or www.excocorp.com.